Omni-Grid® 360
Select another product option
Features
Specifications
Options
Downloads
Features
OMNI-GRID® 360 WELD
BELTS THAT RUN SMOOTHER, STRONGER, LONGER
BELTS THAT RUN SMOOTHER, STRONGER, LONGER
SPIRAL
LOTENSION
HYGENIC
REVOLUTIONARY DESIGN
FOR PARAMOUNT SAFETY
& DURABILITY
REVOLUTIONARY DESIGN FOR PARAMOUNT SAFETY & DURABILITY
The Evolution of Omni-Grid belting continues with the introduction of the 360 Weld on belts that only Ashworth makes. What started as the Omni-Grid is now Omni-Grid 360 where hygiene is built into the belting itself.
The Evolution of Omni-Grid belting continues with the introduction of the 360 Weld on belts that only Ashworth makes. What started as the Omni-Grid is now Omni-Grid 360 where hygiene is built into the belting itself.
INCREASE CAPACITY WHILE MINIMIZING MAINTENANCE COSTS AND DOWNTIME IN YOUR MOST DEMANDING SPIRAL APPLICATIONS WITH OMNI-GRID®
INCREASE CAPACITY WHILE MINIMIZING MAINTENANCE COSTS AND DOWNTIME IN YOUR MOST DEMANDING SPIRAL APPLICATIONS WITH OMNI-GRID®
The Omni-Grid 360 Weld line of belts reduces cage bar wear, maintenance costs and downtime in your most demanding high-tension spiral/turn-curve applications while maintaining belt strength integrity and easy-to-clean/hygienic attributes.
The Omni-Grid 360 Weld line of belts reduces cage bar wear, maintenance costs and downtime in your most demanding high-tension spiral/turn-curve applications while maintaining belt strength integrity and easy-to-clean/hygienic attributes.
HYGIENE BUILT IN
HYGIENE BUILT IN
The increased strength of the Omni-Grid® 360 Weld belts comes from the revolutionary 360° buttonless welds utilizing a patented “zero tension” design which:
The increased strength of the Omni-Grid® 360 Weld belts comes from the revolutionary 360° buttonless welds utilizing a patented “zero tension” design which:
Provides higher product load capacity.
Enables smoother running belts.
Creates less wear on spiral system cage bar caps.
Provides higher product load capacity.
Enables smoother running belts.
Creates less wear on spiral system cage bar caps.
Is formed with a proprietary coining process to prevent break-in wear.
Reduces belt elongation.
Increases belt life.
Is formed with a proprietary coining process to prevent break-in wear.
Reduces belt elongation.
Increases belt life.
Standard with the Omni-Tough Mesh Overlay, originally patented by Ashworth.
Increase capacity while minimizing maintenance costs and downtime in your most demanding spiral applications with Omni-Grid® 360 Weld.
Omni-Grid® 360 Weld Link
Competitor Link
WE BUILD-IN HYGIENE WITH THE PATENTED PRECISION WELD
WE BUILD-IN HYGIENE WITH THE PATENTED PRECISION WELD
The patented, zero-tension, 360° buttonless welds eliminate cracking commonly found with traditional bridge welds. Unlike a traditional bridge weld, the 360°buttonless weld is free from surface imperfections and crevices, which improves hygienic characteristics by eliminating the possibility of bacteria entrapments.
The patented, zero-tension, 360° buttonless welds eliminate cracking commonly found with traditional bridge welds. Unlike a traditional bridge weld, the 360°buttonless weld is free from surface imperfections and crevices, which improves hygienic characteristics by eliminating the possibility of bacteria entrapments.
RESISTANT
TO STICKING
IN FREEZER APPLICATIONS
PROVEN RELIABILITY
PROVEN RELIABILITY
All belts are tested and rated for 100,000 cycles versus competitor ratings of only 50,000 cycles. The 1-inch pitch and 1½-inch pitch Omni-Grid® 360 Weld belts are also offered with integral guard-edges with a smooth rounded finish for applications where product retention is a concern. Available in .75-inch, 1-inch, and 1.5-inch pitch, the Omni-Grid 360 Weld belts are the strongest and longest running grid style belts on the market today
All belts are tested and rated for 100,000 cycles versus competitor ratings of only 50,000 cycles. The 1-inch pitch and 1½-inch pitch Omni-Grid® 360 Weld belts are also offered with integral guard-edges with a smooth rounded finish for applications where product retention is a concern. Available in .75-inch, 1-inch, and 1.5-inch pitch, the Omni-Grid 360 Weld belts are the strongest and longest running grid style belts on the market today
STANDARD FEATURES
STANDARD FEATURES
Omni-Tough Mesh Overlay
21/2 times stronger than conventional overlays and is resistant to product sticking in freezer applications.
Pigtail Spirals
Reduces wire breakage.
OPTIONAL FEATURES
OPTIONAL FEATURES
Integral Guard Edges
Now with smooth, rounded edge finish. Durable and easier to clean than modular guard edges. Available for 1 inch and 1.5 inch pitch belts.
Special Mesh Spirals
A cost effective solution for adding land dividers
DIRECTION
APPLICATIONS
PROVEN RELIABILITY
PROVEN RELIABILITY
All belts are tested and rated for 100,000 cycles versus competitor ratings of only 50,000 cycles. The 1-inch pitch and 1½-inch pitch Omni-Grid® 360 Weld belts are also offered with integral guard-edges with a smooth rounded finish for applications where product retention is a concern. Available in .75-inch, 1-inch, and 1.5-inch pitch, the Omni-Grid 360 Weld belts are the strongest and longest running grid style belts on the market today
STANDARD FEATURES
STANDARD FEATURES
Omni-Tough Mesh Overlay
2-1/2 times stronger than conventional overlays and is resistant to product sticking in freezer applications.
Pigtail Spirals
Reduces wire breakage.
OPTIONAL FEATURES
OPTIONAL FEATURES
Integral Guard Edges
Smooth, rounded edge finish. Durable and easier to clean than modular guard edges. Available for 1 inch and 1.5-inch pitch belts.
Special Mesh Spirals
A cost effective solution for adding land dividers
Specifications
Technical Specifications
Select another product option
Technical Specifications | Units | Omni-Grid® 360 075 |
---|---|---|
Turn Ratio | 2.2-6.0 | |
Pitch | in. [mm] | 0.75 [19.0] |
Available Widths: Curve/Spiral | in. [mm] | 12-40 (304.8-1016) |
Available Widths: Straight Run | in. [mm] | 12-60 (304.8-1524.0) |
Link Height | in. [mm] | 0.44 [11.1] |
Rod Diameter/Material | in. [mm] | 0.192 (4.9) Metal |
Conveying Surface | in. [mm] | Width -2.01 [-51.05] |
Allowable Tension (Curve/Spiral) | lb. [kg] | 150 [68] at 100,000 cycles |
Allowable Tension (Straight Run) | lb. [kg] | 300 [136] at 100,000 cycles |
Turn Direction | Bi-directional | |
Mode of Turning | Inside edge collapses in turn | |
Method of Drive | Sprockets driven on links |
Available Sprocket Options
Sprocket Reference
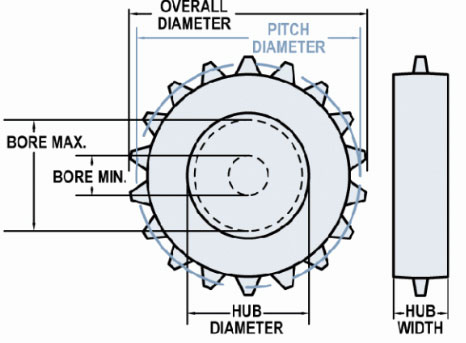
Select another sprocket size
Select a product
Nom. Size | Display | Teeth | Pitch Diameter in (mm) | Hub Diameter in (mm) | Bore Min in (mm) | Bore Max in (mm) |
---|---|---|---|---|---|---|
3 | #3-12 Hardened Steel | 12 | 2.9 (73.66) | 2.36 (59.94) | 1 (25.4) | 1.8 (45.72) |
3 | #3-12 Hardened Steel | 12 | 2.9 (73.66) | 2.36 (59.94) | 1 (25.4) | 1.8 (45.72) |
3 | #3-12 T303 | 12 | 2.9 (73.66) | 2.36 (59.94) | 1 (25.4) | 1.8 (45.72) |
3 | #3-12 T303 | 12 | 2.9 (73.66) | 2.36 (59.94) | 0.94 (23.81) | 1.8 (45.72) |
3 | #3-12 UHMW | 12 | 2.9 (73.66) | 2.25 (57.15) | 0 | 1.5 (38.1) |
3 | #3-16 UHMW | 16 | 3.84 (97.63) | 3 (76.2) | 1.58 (40.01) | 2.13 (54.1) |
3 | #3-16 UHMW | 16 | 3.84 (97.64) | 3 (76.2) | 1 (25.4) | 2.13 (54.1) |
4 | #4-17 T303 | 17 | 4.08 (103.68) | 3.58 (90.81) | 0 | 2.83 (71.88) |
4 | #4-17 UHMW | 17 | 4.08 (103.68) | 3.58 (90.81) | 0.75 (19.05) | 2.58 (65.53) |
4 | #4-17 UHMW | 17 | 4.08 (103.68) | 3.58 (90.81) | 1 (25.4) | 2.58 (65.53) |
4 | #4-18 T303 | 18 | 4.32 (109.68) | 3.82 (96.9) | 0 | 2.95 (74.93) |
4 | #4-18 T303 | 18 | 4.32 (109.68) | 3.82 (96.9) | 1.58 (40.01) | 2.82 (71.63) |
5 | #5-19 UHMW | 19 | 4.56 (115.75) | 4.06 (103.05) | 0.75 (19.05) | 2.94 (74.68) |
5 | #5-21 T303 | 21 | 5.03 (127.81) | 4.54 (115.27) | 1 (25.4) | 3.55 (90.17) |
5 | #5-21 UHMW | 21 | 5.03 (127.81) | 4.54 (115.27) | 1 (25.4) | 3.42 (86.87) |
5 | #5-21 UHMW FS | 21 | 4.79 (121.67) | 4.54 (115.32) | 1 (25.4) | 3.42 (86.87) |
6 | #6 UHMW FI | 0 | 0 | 6 (152.4) | 0.75 (19.05) | 4.64 (117.86) |
6 | #6 UHMW I | 0 | 0 | 6 (152.4) | 0.75 (19.05) | 4.64 (117.86) |
6 | #6-25 T303 | 25 | 5.98 (151.99) | 5.5 (139.67) | 0 | 4.39 (111.51) |
6 | #6-25 T303 | 25 | 5.98 (151.99) | 5.5 (139.67) | 0.5 (12.7) | 4.39 (111.51) |
6 | #6-25 UHMW | 25 | 5.98 (151.99) | 5.5 (139.67) | 0.88 (22.22) | 4.14 (105.16) |
6 | #6-26 T303 | 26 | 6.22 (158.04) | 5.73 (145.64) | 0 | 4.62 (117.35) |
6 | #6-26 T303 | 26 | 6.22 (158.04) | 5.73 (145.64) | 1.58 (40.01) | 4.62 (117.35) |
6 | #6-26 T303 | 26 | 6.22 (158.04) | 5.73 (145.64) | 1.58 (40.01) | 4.62 (117.35) |
6 | #6-26 UHMW | 26 | 6.22 (158.04) | 5.73 (145.64) | 1 (25.4) | 4.37 (111) |
6 | #6-27 UHMW | 27 | 6.42 (163.12) | 5.97 (151.61) | 0.88 (22.22) | 4.61 (117.09) |
8 | #8-34 UHMW | 34 | 8.13 (206.45) | 7.66 (194.46) | 1 (25.4) | 5.93 (150.62) |
Sprockets available in stainless steel, plain steel, and UHMWPE.
UHMWPE material type components have a 150° F (66°C) maximum operation temperature.
Maximum bore sized listed for UHMWPE material is based on 1/2 inch (12.7 mm) of material above keyway.
*Maximum bores provide adequate material thickness for standard keyway. Specify special sized to be used when necessary.
Supports
Support are required at a minimum of 18" apart on load side and 24" maximum on return side. Rollers may also be used. For light loads, support rails may be placed further apart. Consult Ashworth Engineering for assistance.
Material Reference
- Acetal - polyoxymethylene plastic
- Celcon - acetal copolymer
- CI - cast iron
- Hardened Steel
- Nylon
- T303 - stainless steel
- T316 - stainless steel
- UMHW - polyethylene plastic
Belt Calculator
No Results
Base Belt Weight
Belt Pitch
Turn Ratio
Belt Strength
Min Filler Roll Diameter
Conveying Surface
Inside Conveying Surface
Outside Conveying Surface
Mesh Opening Size
Open Area Surface
Open Area Thru
Need more detailed information?
Need more detailed information?
Need more detailed information?
Options
Product Options
High-Density Mesh Overlay
Traditional grid meshes have double the mesh density at the connecting rods. High density mesh consists of spirals with special intermediate loops to create more product support but at the same time reducing the mesh weight allowing for heavier product loads.
Omni-Tough Mesh Overlay
2½ times stronger than conventional
overlays and is resistant to product
sticking in freezer applications
Patented Pigtail Spirals
Reduces wear breakage
Patented Special Mesh Spirals
A cost effective solution for adding
lane dividers or flights
Does this meet your project needs?
Does this meet your project needs?
Does this meet your project needs?
Let’s get started!
Let’s get started!
Let’s get started!
Downloads
Downloads
Technical Bulletins
Installation, Assembly & Maintenance Instructions
Conveyor System Review Form
Illustrations
-
ROD ONLY OG360 WELD 075
-
B18-16-16 OG360 WELD 075
-
B30-16-16 OG360 WELD 075
-
B36-16-16 OG360 WELD 075
-
B42-16-16 OG360 WELD 075
-
B48-16-16 OG360 WELD 075
-
B54-16-16 OG360 WELD 075
-
B72-16-16 OG360 WELD 075
-
ROD ONLY OG360 WELD 100
-
B18-12-16 OG360 WELD 100
-
B24-12-16 OG360 WELD 100
-
B30-12-16 OG360 WELD 100
-
B36-12-16 OG360 WELD 100
-
B42-12-16 OG360 WELD 100
-
B48-12-16 OG360 WELD 100
-
B54-12-16 OG360 WELD 100
-
B60-12-16 OG360 WELD 100
-
B72-12-16 OG360 WELD 100
-
U48-12-17 OG360 WELD 100
-
U60-12-16 OG360 WELD 100
-
U72-12-16 OG360 WELD 100
-
ROD ONLY OG360 WELD 150
-
B18-8-16 OG360 WELD 150
-
B24-8-16 OG360 WELD 150
-
B24-8-17 OG360 WELD 150 IGE
-
B30-8-16 OG360 WELD 150
-
B36-8-16 OG360 WELD 150
-
B42-8-16 OG360 WELD 150
-
B54-8-16 OG360 WELD 150
-
B72-8-17 OG360 WELD 150
-
U48-8-16 OG360 WELD 150
-
U54-8-17 OG360 WELD 150
-
OG360 100 H96 12 17
-
OG360 100 Rod Only
-
OG360 100 U48 12 17
-
OG360 100 U54 12 16
-
OG360 100 U54 12 17
-
OG360 100 U60 12 16
-
OG360 100 U60 12 17
-
OG360 100 U72 12 16
-
OG360 100 U72 12 17
-
OG360 150 B18 8 16
-
OG360 150 B18 8 17
-
OG360 150 B24 8 16
-
OG360 150 B24 8 17
-
OG360 150 B30 8 16
-
OG360 150 B30 8 17
-
OG360 150 B36 8 16
-
OG360 150 B36 8 17
-
OG360 150 B42 8 16
-
OG360 150 B42 8 17
-
OG360 150 B54 8 16
-
OG360 150 B54 8 17
-
OG360 150 B72 8 17
-
OG360 150 Rod Only
-
OG360 150 U36 8 16
-
OG360 150 U48 8 16
-
OG360 150 U48 8 17
-
OG360 150 U54 8 16
-
OG360 150 U54 8 17
-
OG360 075 B18 16 16
-
OG360 075 B24 16 16
-
OG360 075 B24 16 17
-
OG360 075 B30 16 16
-
OG360 075 B30 16 17
-
OG360 075 B36 16 16
-
OG360 075 B36 16 17
-
OG360 075 B42 16 16
-
OG360 075 B42 16 17
-
OG360 075 B48 16 16
-
OG360 075 B48 16 17
-
OG360 075 B54 16 16
-
OG360 075 B54 16 17
-
OG360 075 B60 16 16
-
OG360 075 B60 16 17
-
OG360 075 B72 16 16
-
OG360 075 B72 16 17
-
OG360 075 H106 16 16
-
OG360 075 H106 16 17
-
OG360 075 H60 16 16
-
OG360 075 H60 16 17
-
OG360 075 H72 16 16
-
OG360 075 H72 16 17
-
OG360 075 H84 16 16
-
OG360 075 H84 16 17
-
OG360 075 H96 16 16
-
OG360 075 H96 16 17
-
OG360 075 NO MESH
-
OG360 075 Rod Only
-
OG360 075 U36 16 16
-
OG360 100 B30 12 17
-
OG360 100 B18 12 16
-
OG360 100 B18 12 17
-
OG360 100 B24 12 16
-
OG360 100 B24 12 17
-
OG360 100 B30 12 16
-
OG360 100 B36 12 16
-
OG360 100 B36 12 17
-
OG360 100 B42 12 16
-
OG360 100 B42 12 17
-
OG360 100 B48 12 16
-
OG360 100 B48 12 17
-
OG360 100 B54 12 16
-
OG360 100 B54 12 17
-
OG360 100 B60 12 16
-
OG360 100 B60 12 17
-
OG360 100 B72 12 16
-
OG360 100 B72 12 17
-
OG360 100 H106 12 16
-
OG360 100 H106 12 17
-
OG360 100 H60 12 16
-
OG360 100 H60 12 17
-
OG360 100 H72 12 16
-
OG360 100 H72 12 17
-
OG360 100 H84 12 16
-
OG360 100 H84 12 17
-
OG360 100 H96 12 16
Features
OMNI-GRID® 360 WELD
BELTS THAT RUN SMOOTHER, STRONGER, LONGER
BELTS THAT RUN SMOOTHER, STRONGER, LONGER
SPIRAL
LOTENSION
HYGENIC
REVOLUTIONARY DESIGN
FOR PARAMOUNT SAFETY
& DURABILITY
REVOLUTIONARY DESIGN FOR PARAMOUNT SAFETY & DURABILITY
The Evolution of Omni-Grid belting continues with the introduction of the 360 Weld on belts that only Ashworth makes. What started as the Omni-Grid is now Omni-Grid 360 where hygiene is built into the belting itself.
The Evolution of Omni-Grid belting continues with the introduction of the 360 Weld on belts that only Ashworth makes. What started as the Omni-Grid is now Omni-Grid 360 where hygiene is built into the belting itself.
INCREASE CAPACITY WHILE MINIMIZING MAINTENANCE COSTS AND DOWNTIME IN YOUR MOST DEMANDING SPIRAL APPLICATIONS WITH OMNI-GRID®
INCREASE CAPACITY WHILE MINIMIZING MAINTENANCE COSTS AND DOWNTIME IN YOUR MOST DEMANDING SPIRAL APPLICATIONS WITH OMNI-GRID®
The Omni-Grid 360 Weld line of belts reduces cage bar wear, maintenance costs and downtime in your most demanding high-tension spiral/turn-curve applications while maintaining belt strength integrity and easy-to-clean/hygienic attributes.
The Omni-Grid 360 Weld line of belts reduces cage bar wear, maintenance costs and downtime in your most demanding high-tension spiral/turn-curve applications while maintaining belt strength integrity and easy-to-clean/hygienic attributes.
HYGIENE BUILT IN
HYGIENE BUILT IN
The increased strength of the Omni-Grid® 360 Weld belts comes from the revolutionary 360° buttonless welds utilizing a patented “zero tension” design which:
The increased strength of the Omni-Grid® 360 Weld belts comes from the revolutionary 360° buttonless welds utilizing a patented “zero tension” design which:
Provides higher product load capacity.
Enables smoother running belts.
Creates less wear on spiral system cage bar caps.
Provides higher product load capacity.
Enables smoother running belts.
Creates less wear on spiral system cage bar caps.
Is formed with a proprietary coining process to prevent break-in wear.
Reduces belt elongation.
Increases belt life.
Is formed with a proprietary coining process to prevent break-in wear.
Reduces belt elongation.
Increases belt life.
Standard with the Omni-Tough Mesh Overlay, originally patented by Ashworth.
Increase capacity while minimizing maintenance costs and downtime in your most demanding spiral applications with Omni-Grid® 360 Weld.
Omni-Grid® 360 Weld Link
Competitor Link
WE BUILD-IN HYGIENE WITH THE PATENTED PRECISION WELD
WE BUILD-IN HYGIENE WITH THE PATENTED PRECISION WELD
The patented, zero-tension, 360° buttonless welds eliminate cracking commonly found with traditional bridge welds. Unlike a traditional bridge weld, the 360°buttonless weld is free from surface imperfections and crevices, which improves hygienic characteristics by eliminating the possibility of bacteria entrapments.
The patented, zero-tension, 360° buttonless welds eliminate cracking commonly found with traditional bridge welds. Unlike a traditional bridge weld, the 360°buttonless weld is free from surface imperfections and crevices, which improves hygienic characteristics by eliminating the possibility of bacteria entrapments.
RESISTANT
TO STICKING
IN FREEZER APPLICATIONS
PROVEN RELIABILITY
PROVEN RELIABILITY
All belts are tested and rated for 100,000 cycles versus competitor ratings of only 50,000 cycles. The 1-inch pitch and 1½-inch pitch Omni-Grid® 360 Weld belts are also offered with integral guard-edges with a smooth rounded finish for applications where product retention is a concern. Available in .75-inch, 1-inch, and 1.5-inch pitch, the Omni-Grid 360 Weld belts are the strongest and longest running grid style belts on the market today
All belts are tested and rated for 100,000 cycles versus competitor ratings of only 50,000 cycles. The 1-inch pitch and 1½-inch pitch Omni-Grid® 360 Weld belts are also offered with integral guard-edges with a smooth rounded finish for applications where product retention is a concern. Available in .75-inch, 1-inch, and 1.5-inch pitch, the Omni-Grid 360 Weld belts are the strongest and longest running grid style belts on the market today
STANDARD FEATURES
STANDARD FEATURES
Omni-Tough Mesh Overlay
21/2 times stronger than conventional overlays and is resistant to product sticking in freezer applications.
Pigtail Spirals
Reduces wire breakage.
OPTIONAL FEATURES
OPTIONAL FEATURES
Integral Guard Edges
Now with smooth, rounded edge finish. Durable and easier to clean than modular guard edges. Available for 1 inch and 1.5 inch pitch belts.
Special Mesh Spirals
A cost effective solution for adding land dividers
DIRECTION
APPLICATIONS
PROVEN RELIABILITY
PROVEN RELIABILITY
All belts are tested and rated for 100,000 cycles versus competitor ratings of only 50,000 cycles. The 1-inch pitch and 1½-inch pitch Omni-Grid® 360 Weld belts are also offered with integral guard-edges with a smooth rounded finish for applications where product retention is a concern. Available in .75-inch, 1-inch, and 1.5-inch pitch, the Omni-Grid 360 Weld belts are the strongest and longest running grid style belts on the market today
STANDARD FEATURES
STANDARD FEATURES
Omni-Tough Mesh Overlay
2-1/2 times stronger than conventional overlays and is resistant to product sticking in freezer applications.
Pigtail Spirals
Reduces wire breakage.
OPTIONAL FEATURES
OPTIONAL FEATURES
Integral Guard Edges
Smooth, rounded edge finish. Durable and easier to clean than modular guard edges. Available for 1 inch and 1.5-inch pitch belts.
Special Mesh Spirals
A cost effective solution for adding land dividers
Specifications
Technical Specifications
Select another product option
Technical Specifications | Units | Omni-Grid® 360 100 |
---|---|---|
Turn Ratio | 1.7-6.0 | |
Pitch | in. [mm] | 1.08 [27.4] |
Available Widths: Curve/Spiral | in. [mm] | 12-40 (304.8-1016) |
Available Widths: Straight Run | in. [mm] | 12-48 (304.8-1219.2) |
Link Height | in. [mm] | 0.50 [12.7] |
Rod Diameter/Material | in. [mm] | 0.192 (4.9) Metal |
Conveying Surface | in. [mm] | Width -2.53 [-64.26] |
Allowable Tension (Curve/Spiral) | lb. [kg] | 200 [91] at 100,000 cycles |
Allowable Tension (Straight Run) | lb. [kg] | 400 [181] at 100,000 cycles |
Turn Direction | Bi-directional | |
Mode of Turning | Inside edge collapses in turn | |
Method of Drive | Sprockets driven on links |
Available Sprocket Options
Sprocket Reference
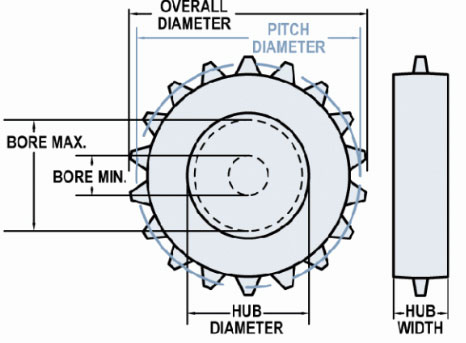
Select another sprocket size
Select a product
Nom. Size | Display | Teeth | Pitch Diameter in (mm) | Hub Diameter in (mm) | Bore Min in (mm) | Bore Max in (mm) |
---|---|---|---|---|---|---|
3 | #3-9 Hardened Steel | 9 | 0 | 2.45 (62.23) | 1 (25.4) | 1.83 (46.48) |
3 | #3-9 T303 | 9 | 3.16 (80.26) | 2.46 (62.48) | 1 (25.4) | 1.84 (46.74) |
3 | #3-9 T303 | 9 | 3.16 (80.26) | 2.46 (62.48) | 1 (25.4) | 1.84 (46.74) |
3 | #3-9 T303 | 9 | 3.16 (80.26) | 2.46 (62.48) | 1.25 (31.75) | 1.84 (46.74) |
3 | #3-9 T303 | 9 | 3.16 (80.26) | 2.46 (62.48) | 0.94 (23.81) | 1.84 (46.74) |
3 | #3-9 T316 | 9 | 3.16 (80.26) | 2.46 (62.48) | 1.44 (36.51) | 1.84 (46.74) |
3 | #3-9 UHMW | 9 | 3.16 (80.26) | 2.53 (64.26) | 1 (25.4) | 1.72 (43.69) |
3 | #3-9 UHMW | 9 | 3.16 (80.26) | 2.53 (64.26) | 0 | 1.72 (43.69) |
4 | #4 UHMW FI | 0 | 0 | 3.92 (99.57) | 0.75 (19.05) | 2.93 (74.42) |
4 | #4 UHMW I | 0 | 0 | 3.92 (99.57) | 0 | 2.93 (74.42) |
4 | #4-11 T303 | 11 | 3.83 (97.36) | 3.18 (80.72) | 0 | 2.07 (52.58) |
4 | #4-11 T303 | 11 | 3.83 (97.36) | 3.18 (80.72) | 0 | 2.44 (61.98) |
4 | #4-12 T303 | 12 | 4.17 (105.97) | 3.54 (89.92) | 0 | 2.8 (71.12) |
4 | #4-12 T316 | 12 | 4.17 (105.97) | 3.54 (89.92) | 0 | 2.8 (71.12) |
4 | #4-12 UHMW | 12 | 4.17 (105.97) | 3.45 (87.63) | 0.75 (19.05) | 2.46 (62.48) |
4 | #4-13 Celcon | 13 | 4.4 (111.76) | 3.9 (99.06) | 1 (25.4) | 2.91 (73.91) |
4 | #4-13 CI | 13 | 4.53 (115.09) | 3.91 (99.22) | 0 | 3.04 (77.22) |
4 | #4-13 T316 | 13 | 4.53 (115.09) | 3.91 (99.22) | 0 | 3.04 (77.22) |
4 | #4-13 UHMW | 13 | 4.53 (115.06) | 3.9 (99.06) | 1 (25.4) | 2.91 (73.91) |
5 | #5-15 T303 | 15 | 5.2 (131.95) | 4.58 (116.36) | 0 | 3.59 (91.19) |
5 | #5-15 UHMW | 15 | 5.2 (131.95) | 4.58 (116.36) | 2 (50.8) | 3.46 (87.88) |
6 | #6 UHMW FI | 0 | 0 | 5.65 (143.51) | 0.75 (19.05) | 4.29 (108.97) |
6 | #6 UHMW I | 0 | 0 | 5.65 (143.51) | 0 | 4.29 (108.97) |
6 | #6-18 CI | 18 | 6.24 (158.5) | 5.66 (143.67) | 0 | 3.75 (95.25) |
6 | #6-18 Nylon | 18 | 6.24 (158.5) | 5.65 (143.51) | 1 (25.4) | 4.54 (115.32) |
6 | #6-18 T316 | 18 | 6.24 (158.5) | 5.66 (143.67) | 1 (25.4) | 3.75 (95.25) |
6 | #6-18 UHMW | 18 | 6.24 (158.5) | 5.65 (143.51) | 0 | 4.29 (108.97) |
6 | #6-18 UHMW FS | 18 | 6.15 (156.16) | 5.65 (143.46) | 0 | 4.29 (108.97) |
6 | #6-18 UHMW Product Release | 18 | 6.4 (162.51) | 5.65 (143.46) | 1 (25.4) | 4.29 (108.97) |
6 | #6-18 UHMW Split | 18 | 6.24 (158.5) | 5.65 (143.46) | 0 | 4.29 (108.97) |
6 | #6-19 T303 | 19 | 6.55 (166.47) | 6.03 (153.21) | 0 | 4.8 (121.92) |
6 | #6-19 UHMW | 19 | 6.55 (166.47) | 6.03 (153.21) | 1.18 (30) | 4.67 (118.62) |
8 | #8 UHMW FI | 0 | 0 | 7.38 (187.45) | 0.75 (19.05) | 5.89 (149.61) |
8 | #8 UHMW I | 0 | 0 | 7.38 (187.45) | 0 | 5.89 (149.61) |
8 | #8-23 CI | 23 | 7.41 (188.11) | 7.41 (188.11) | 0 | 5.9 (149.86) |
8 | #8-23 CI | 23 | 7.96 (202.18) | 7.41 (188.12) | 0 | 4.75 (120.65) |
8 | #8-23 T316 | 23 | 7.96 (202.18) | 7.41 (188.12) | 0 | 4.75 (120.65) |
8 | #8-23 T316 | 23 | 7.97 (202.41) | 7.41 (188.12) | 1 (25.4) | 4.75 (120.65) |
8 | #8-23 UHMW | 23 | 7.96 (202.18) | 7.39 (187.71) | 1 (25.4) | 5.9 (149.86) |
8 | #8-23 UHMW Split | 23 | 7.89 (200.33) | 7.39 (187.63) | 0 | 5.9 (149.86) |
10 | #10-31 CI | 31 | 10.72 (272.29) | 10.16 (258.06) | 0 | 8.67 (220.22) |
10 | #10-31 T316 | 31 | 10.72 (272.29) | 10.16 (258.06) | 0 | 8.67 (220.22) |
10 | #10-31 UHMW | 31 | 10.66 (270.76) | 10.16 (258.06) | 0.99 (25.02) | 8.42 (213.87) |
12 | #12-37 UHMW | 37 | 12.74 (323.49) | 12.24 (310.79) | 0.99 (25.02) | 10.49 (266.45) |
UHMWPE material type components have a 150° F (66°C) maximum operation temperature.
Maximum bore sized listed for UHMWPE material is based on 1/2 inch (12.7 mm) of material above keyway.
Supports
Support are required at a minimum of 18" apart on load side and 24" maximum on return side. Rollers may also be used. For light loads, support rails may be placed further apart. Consult Ashworth Engineering for assistance.
Material Reference
- Acetal - polyoxymethylene plastic
- Celcon - acetal copolymer
- CI - cast iron
- Hardened Steel
- Nylon
- T303 - stainless steel
- T316 - stainless steel
- UMHW - polyethylene plastic
Belt Calculator
No Results
Base Belt Weight
Belt Pitch
Turn Ratio
Belt Strength
Min Filler Roll Diameter
Conveying Surface
Inside Conveying Surface
Outside Conveying Surface
Mesh Opening Size
Open Area Surface
Open Area Thru
Need more detailed information?
Need more detailed information?
Need more detailed information?
Options
Product Options
High-Density Mesh Overlay
Traditional grid meshes have double the mesh density at the connecting rods. High density mesh consists of spirals with special intermediate loops to create more product support but at the same time reducing the mesh weight allowing for heavier product loads.
Omni-Tough Mesh Overlay
2½ times stronger than conventional
overlays and is resistant to product
sticking in freezer applications
Patented Pigtail Spirals
Reduces wear breakage
Patented Special Mesh Spirals
A cost effective solution for adding
lane dividers or flights
Does this meet your project needs?
Does this meet your project needs?
Does this meet your project needs?
Let’s get started!
Let’s get started!
Let’s get started!
Downloads
Downloads
Technical Bulletins
Installation, Assembly & Maintenance Instructions
Conveyor System Review Form
Illustrations
-
ROD ONLY OG360 WELD 075
-
B18-16-16 OG360 WELD 075
-
B30-16-16 OG360 WELD 075
-
B36-16-16 OG360 WELD 075
-
B42-16-16 OG360 WELD 075
-
B48-16-16 OG360 WELD 075
-
B54-16-16 OG360 WELD 075
-
B72-16-16 OG360 WELD 075
-
ROD ONLY OG360 WELD 100
-
B18-12-16 OG360 WELD 100
-
B24-12-16 OG360 WELD 100
-
B30-12-16 OG360 WELD 100
-
B36-12-16 OG360 WELD 100
-
B42-12-16 OG360 WELD 100
-
B48-12-16 OG360 WELD 100
-
B54-12-16 OG360 WELD 100
-
B60-12-16 OG360 WELD 100
-
B72-12-16 OG360 WELD 100
-
U48-12-17 OG360 WELD 100
-
U60-12-16 OG360 WELD 100
-
U72-12-16 OG360 WELD 100
-
ROD ONLY OG360 WELD 150
-
B18-8-16 OG360 WELD 150
-
B24-8-16 OG360 WELD 150
-
B24-8-17 OG360 WELD 150 IGE
-
B30-8-16 OG360 WELD 150
-
B36-8-16 OG360 WELD 150
-
B42-8-16 OG360 WELD 150
-
B54-8-16 OG360 WELD 150
-
B72-8-17 OG360 WELD 150
-
U48-8-16 OG360 WELD 150
-
U54-8-17 OG360 WELD 150
-
OG360 100 H96 12 17
-
OG360 100 Rod Only
-
OG360 100 U48 12 17
-
OG360 100 U54 12 16
-
OG360 100 U54 12 17
-
OG360 100 U60 12 16
-
OG360 100 U60 12 17
-
OG360 100 U72 12 16
-
OG360 100 U72 12 17
-
OG360 150 B18 8 16
-
OG360 150 B18 8 17
-
OG360 150 B24 8 16
-
OG360 150 B24 8 17
-
OG360 150 B30 8 16
-
OG360 150 B30 8 17
-
OG360 150 B36 8 16
-
OG360 150 B36 8 17
-
OG360 150 B42 8 16
-
OG360 150 B42 8 17
-
OG360 150 B54 8 16
-
OG360 150 B54 8 17
-
OG360 150 B72 8 17
-
OG360 150 Rod Only
-
OG360 150 U36 8 16
-
OG360 150 U48 8 16
-
OG360 150 U48 8 17
-
OG360 150 U54 8 16
-
OG360 150 U54 8 17
-
OG360 075 B18 16 16
-
OG360 075 B24 16 16
-
OG360 075 B24 16 17
-
OG360 075 B30 16 16
-
OG360 075 B30 16 17
-
OG360 075 B36 16 16
-
OG360 075 B36 16 17
-
OG360 075 B42 16 16
-
OG360 075 B42 16 17
-
OG360 075 B48 16 16
-
OG360 075 B48 16 17
-
OG360 075 B54 16 16
-
OG360 075 B54 16 17
-
OG360 075 B60 16 16
-
OG360 075 B60 16 17
-
OG360 075 B72 16 16
-
OG360 075 B72 16 17
-
OG360 075 H106 16 16
-
OG360 075 H106 16 17
-
OG360 075 H60 16 16
-
OG360 075 H60 16 17
-
OG360 075 H72 16 16
-
OG360 075 H72 16 17
-
OG360 075 H84 16 16
-
OG360 075 H84 16 17
-
OG360 075 H96 16 16
-
OG360 075 H96 16 17
-
OG360 075 NO MESH
-
OG360 075 Rod Only
-
OG360 075 U36 16 16
-
OG360 100 B30 12 17
-
OG360 100 B18 12 16
-
OG360 100 B18 12 17
-
OG360 100 B24 12 16
-
OG360 100 B24 12 17
-
OG360 100 B30 12 16
-
OG360 100 B36 12 16
-
OG360 100 B36 12 17
-
OG360 100 B42 12 16
-
OG360 100 B42 12 17
-
OG360 100 B48 12 16
-
OG360 100 B48 12 17
-
OG360 100 B54 12 16
-
OG360 100 B54 12 17
-
OG360 100 B60 12 16
-
OG360 100 B60 12 17
-
OG360 100 B72 12 16
-
OG360 100 B72 12 17
-
OG360 100 H106 12 16
-
OG360 100 H106 12 17
-
OG360 100 H60 12 16
-
OG360 100 H60 12 17
-
OG360 100 H72 12 16
-
OG360 100 H72 12 17
-
OG360 100 H84 12 16
-
OG360 100 H84 12 17
-
OG360 100 H96 12 16
Features
OMNI-GRID® 360 WELD
BELTS THAT RUN SMOOTHER, STRONGER, LONGER
BELTS THAT RUN SMOOTHER, STRONGER, LONGER
SPIRAL
LOTENSION
HYGENIC
REVOLUTIONARY DESIGN
FOR PARAMOUNT SAFETY
& DURABILITY
REVOLUTIONARY DESIGN FOR PARAMOUNT SAFETY & DURABILITY
The Evolution of Omni-Grid belting continues with the introduction of the 360 Weld on belts that only Ashworth makes. What started as the Omni-Grid is now Omni-Grid 360 where hygiene is built into the belting itself.
The Evolution of Omni-Grid belting continues with the introduction of the 360 Weld on belts that only Ashworth makes. What started as the Omni-Grid is now Omni-Grid 360 where hygiene is built into the belting itself.
INCREASE CAPACITY WHILE MINIMIZING MAINTENANCE COSTS AND DOWNTIME IN YOUR MOST DEMANDING SPIRAL APPLICATIONS WITH OMNI-GRID®
INCREASE CAPACITY WHILE MINIMIZING MAINTENANCE COSTS AND DOWNTIME IN YOUR MOST DEMANDING SPIRAL APPLICATIONS WITH OMNI-GRID®
The Omni-Grid 360 Weld line of belts reduces cage bar wear, maintenance costs and downtime in your most demanding high-tension spiral/turn-curve applications while maintaining belt strength integrity and easy-to-clean/hygienic attributes.
The Omni-Grid 360 Weld line of belts reduces cage bar wear, maintenance costs and downtime in your most demanding high-tension spiral/turn-curve applications while maintaining belt strength integrity and easy-to-clean/hygienic attributes.
HYGIENE BUILT IN
HYGIENE BUILT IN
The increased strength of the Omni-Grid® 360 Weld belts comes from the revolutionary 360° buttonless welds utilizing a patented “zero tension” design which:
The increased strength of the Omni-Grid® 360 Weld belts comes from the revolutionary 360° buttonless welds utilizing a patented “zero tension” design which:
Provides higher product load capacity.
Enables smoother running belts.
Creates less wear on spiral system cage bar caps.
Provides higher product load capacity.
Enables smoother running belts.
Creates less wear on spiral system cage bar caps.
Is formed with a proprietary coining process to prevent break-in wear.
Reduces belt elongation.
Increases belt life.
Is formed with a proprietary coining process to prevent break-in wear.
Reduces belt elongation.
Increases belt life.
Standard with the Omni-Tough Mesh Overlay, originally patented by Ashworth.
Increase capacity while minimizing maintenance costs and downtime in your most demanding spiral applications with Omni-Grid® 360 Weld.
Omni-Grid® 360 Weld Link
Competitor Link
WE BUILD-IN HYGIENE WITH THE PATENTED PRECISION WELD
WE BUILD-IN HYGIENE WITH THE PATENTED PRECISION WELD
The patented, zero-tension, 360° buttonless welds eliminate cracking commonly found with traditional bridge welds. Unlike a traditional bridge weld, the 360°buttonless weld is free from surface imperfections and crevices, which improves hygienic characteristics by eliminating the possibility of bacteria entrapments.
The patented, zero-tension, 360° buttonless welds eliminate cracking commonly found with traditional bridge welds. Unlike a traditional bridge weld, the 360°buttonless weld is free from surface imperfections and crevices, which improves hygienic characteristics by eliminating the possibility of bacteria entrapments.
RESISTANT
TO STICKING
IN FREEZER APPLICATIONS
PROVEN RELIABILITY
PROVEN RELIABILITY
All belts are tested and rated for 100,000 cycles versus competitor ratings of only 50,000 cycles. The 1-inch pitch and 1½-inch pitch Omni-Grid® 360 Weld belts are also offered with integral guard-edges with a smooth rounded finish for applications where product retention is a concern. Available in .75-inch, 1-inch, and 1.5-inch pitch, the Omni-Grid 360 Weld belts are the strongest and longest running grid style belts on the market today
All belts are tested and rated for 100,000 cycles versus competitor ratings of only 50,000 cycles. The 1-inch pitch and 1½-inch pitch Omni-Grid® 360 Weld belts are also offered with integral guard-edges with a smooth rounded finish for applications where product retention is a concern. Available in .75-inch, 1-inch, and 1.5-inch pitch, the Omni-Grid 360 Weld belts are the strongest and longest running grid style belts on the market today
STANDARD FEATURES
STANDARD FEATURES
Omni-Tough Mesh Overlay
21/2 times stronger than conventional overlays and is resistant to product sticking in freezer applications.
Pigtail Spirals
Reduces wire breakage.
OPTIONAL FEATURES
OPTIONAL FEATURES
Integral Guard Edges
Now with smooth, rounded edge finish. Durable and easier to clean than modular guard edges. Available for 1 inch and 1.5 inch pitch belts.
Special Mesh Spirals
A cost effective solution for adding land dividers
DIRECTION
APPLICATIONS
PROVEN RELIABILITY
PROVEN RELIABILITY
All belts are tested and rated for 100,000 cycles versus competitor ratings of only 50,000 cycles. The 1-inch pitch and 1½-inch pitch Omni-Grid® 360 Weld belts are also offered with integral guard-edges with a smooth rounded finish for applications where product retention is a concern. Available in .75-inch, 1-inch, and 1.5-inch pitch, the Omni-Grid 360 Weld belts are the strongest and longest running grid style belts on the market today
STANDARD FEATURES
STANDARD FEATURES
Omni-Tough Mesh Overlay
2-1/2 times stronger than conventional overlays and is resistant to product sticking in freezer applications.
Pigtail Spirals
Reduces wire breakage.
OPTIONAL FEATURES
OPTIONAL FEATURES
Integral Guard Edges
Smooth, rounded edge finish. Durable and easier to clean than modular guard edges. Available for 1 inch and 1.5-inch pitch belts.
Special Mesh Spirals
A cost effective solution for adding land dividers
Specifications
Technical Specifications
Select another product option
Technical Specifications | Units | Omni-Grid® 360 150 |
---|---|---|
Turn Ratio | 1.6-6.0 | |
Pitch | in. [mm] | 1.50 [38.1] |
Available Widths: Curve/Spiral | in. [mm] | 12-54 (304.8-1372) |
Available Widths: Straight Run | in. [mm] | 12-60 (304.8-1524.0) |
Link Height | in. [mm] | 0.59 [15.0] |
Rod Diameter/Material | in. [mm] | 0.236 (6.0) Metal |
Conveying Surface | in. [mm] | Width -2.94 [-74.68] |
Allowable Tension (Curve/Spiral) | lb. [kg] | 400 [181] at 100,000 cycles |
Allowable Tension (Straight Run) | lb. [kg] | 800 [363] at 100,000 cycles |
Turn Direction | Bi-directional | |
Mode of Turning | Inside edge collapses in turn | |
Method of Drive | Sprockets driven on links |
Available Sprocket Options
Sprocket Reference
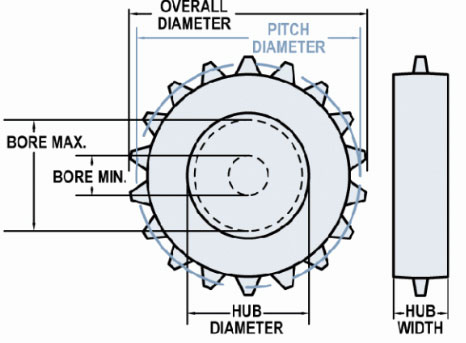
Select another sprocket size
Select a product
Nom. Size | Display | Teeth | Pitch Diameter in (mm) | Hub Diameter in (mm) | Bore Min in (mm) | Bore Max in (mm) |
---|---|---|---|---|---|---|
6 | #6 UHMW FI | 0 | 0 | 5.5 (139.7) | 0.75 (19.05) | 4.14 (105.16) |
6 | #6 UHMW I | 0 | 0 | 5.5 (139.7) | 0.75 (19.05) | 4.14 (105.16) |
6 | #6-13 UHMW Not Recommended | 13 | 6.27 (159.26) | 5.5 (139.7) | 0 | 4.14 (105.16) |
8 | #8 UHMW FI | 0 | 0 | 7.43 (188.72) | 0 | 5.94 (150.88) |
8 | #8 UHMW I | 0 | 0 | 7.43 (188.72) | 0.75 (19.05) | 5.94 (150.88) |
8 | #8-17 T303 | 17 | 8.16 (207.26) | 7.43 (188.72) | 0 | 5.95 (151.13) |
8 | #8-17 UHMW | 17 | 8.16 (207.26) | 7.43 (188.72) | 0.75 (19.05) | 5.94 (150.88) |
UHMWPE material type components have a 150° F (66°C) maximum operation temperature.
Maximum bore sized listed for UHMWPE material is based on 1/2 inch (12.7 mm) of material above keyway.
Supports
Supports are required at a minimum of 18" apart on load side and 24" maximum on return side. Rollers may also be used. For light loads, support rails may be placed further apart. Consult Ashworth Engineering for assistance.
Material Reference
- Acetal - polyoxymethylene plastic
- Celcon - acetal copolymer
- CI - cast iron
- Hardened Steel
- Nylon
- T303 - stainless steel
- T316 - stainless steel
- UMHW - polyethylene plastic
Belt Calculator
No Results
Base Belt Weight
Belt Pitch
Turn Ratio
Belt Strength
Min Filler Roll Diameter
Conveying Surface
Inside Conveying Surface
Outside Conveying Surface
Mesh Opening Size
Open Area Surface
Open Area Thru
Need more detailed information?
Need more detailed information?
Need more detailed information?
Options
Product Options
High-Density Mesh Overlay
Traditional grid meshes have double the mesh density at the connecting rods. High density mesh consists of spirals with special intermediate loops to create more product support but at the same time reducing the mesh weight allowing for heavier product loads.
Omni-Tough Mesh Overlay
2½ times stronger than conventional
overlays and is resistant to product
sticking in freezer applications
Patented Pigtail Spirals
Reduces wear breakage
Patented Special Mesh Spirals
A cost effective solution for adding
lane dividers or flights
Does this meet your project needs?
Does this meet your project needs?
Does this meet your project needs?
Let’s get started!
Let’s get started!
Let’s get started!
Downloads
Downloads
Technical Bulletins
Installation, Assembly & Maintenance Instructions
Conveyor System Review Form
Illustrations
-
ROD ONLY OG360 WELD 075
-
B18-16-16 OG360 WELD 075
-
B30-16-16 OG360 WELD 075
-
B36-16-16 OG360 WELD 075
-
B42-16-16 OG360 WELD 075
-
B48-16-16 OG360 WELD 075
-
B54-16-16 OG360 WELD 075
-
B72-16-16 OG360 WELD 075
-
ROD ONLY OG360 WELD 100
-
B18-12-16 OG360 WELD 100
-
B24-12-16 OG360 WELD 100
-
B30-12-16 OG360 WELD 100
-
B36-12-16 OG360 WELD 100
-
B42-12-16 OG360 WELD 100
-
B48-12-16 OG360 WELD 100
-
B54-12-16 OG360 WELD 100
-
B60-12-16 OG360 WELD 100
-
B72-12-16 OG360 WELD 100
-
U48-12-17 OG360 WELD 100
-
U60-12-16 OG360 WELD 100
-
U72-12-16 OG360 WELD 100
-
ROD ONLY OG360 WELD 150
-
B18-8-16 OG360 WELD 150
-
B24-8-16 OG360 WELD 150
-
B24-8-17 OG360 WELD 150 IGE
-
B30-8-16 OG360 WELD 150
-
B36-8-16 OG360 WELD 150
-
B42-8-16 OG360 WELD 150
-
B54-8-16 OG360 WELD 150
-
B72-8-17 OG360 WELD 150
-
U48-8-16 OG360 WELD 150
-
U54-8-17 OG360 WELD 150
-
OG360 100 H96 12 17
-
OG360 100 Rod Only
-
OG360 100 U48 12 17
-
OG360 100 U54 12 16
-
OG360 100 U54 12 17
-
OG360 100 U60 12 16
-
OG360 100 U60 12 17
-
OG360 100 U72 12 16
-
OG360 100 U72 12 17
-
OG360 150 B18 8 16
-
OG360 150 B18 8 17
-
OG360 150 B24 8 16
-
OG360 150 B24 8 17
-
OG360 150 B30 8 16
-
OG360 150 B30 8 17
-
OG360 150 B36 8 16
-
OG360 150 B36 8 17
-
OG360 150 B42 8 16
-
OG360 150 B42 8 17
-
OG360 150 B54 8 16
-
OG360 150 B54 8 17
-
OG360 150 B72 8 17
-
OG360 150 Rod Only
-
OG360 150 U36 8 16
-
OG360 150 U48 8 16
-
OG360 150 U48 8 17
-
OG360 150 U54 8 16
-
OG360 150 U54 8 17
-
OG360 075 B18 16 16
-
OG360 075 B24 16 16
-
OG360 075 B24 16 17
-
OG360 075 B30 16 16
-
OG360 075 B30 16 17
-
OG360 075 B36 16 16
-
OG360 075 B36 16 17
-
OG360 075 B42 16 16
-
OG360 075 B42 16 17
-
OG360 075 B48 16 16
-
OG360 075 B48 16 17
-
OG360 075 B54 16 16
-
OG360 075 B54 16 17
-
OG360 075 B60 16 16
-
OG360 075 B60 16 17
-
OG360 075 B72 16 16
-
OG360 075 B72 16 17
-
OG360 075 H106 16 16
-
OG360 075 H106 16 17
-
OG360 075 H60 16 16
-
OG360 075 H60 16 17
-
OG360 075 H72 16 16
-
OG360 075 H72 16 17
-
OG360 075 H84 16 16
-
OG360 075 H84 16 17
-
OG360 075 H96 16 16
-
OG360 075 H96 16 17
-
OG360 075 NO MESH
-
OG360 075 Rod Only
-
OG360 075 U36 16 16
-
OG360 100 B30 12 17
-
OG360 100 B18 12 16
-
OG360 100 B18 12 17
-
OG360 100 B24 12 16
-
OG360 100 B24 12 17
-
OG360 100 B30 12 16
-
OG360 100 B36 12 16
-
OG360 100 B36 12 17
-
OG360 100 B42 12 16
-
OG360 100 B42 12 17
-
OG360 100 B48 12 16
-
OG360 100 B48 12 17
-
OG360 100 B54 12 16
-
OG360 100 B54 12 17
-
OG360 100 B60 12 16
-
OG360 100 B60 12 17
-
OG360 100 B72 12 16
-
OG360 100 B72 12 17
-
OG360 100 H106 12 16
-
OG360 100 H106 12 17
-
OG360 100 H60 12 16
-
OG360 100 H60 12 17
-
OG360 100 H72 12 16
-
OG360 100 H72 12 17
-
OG360 100 H84 12 16
-
OG360 100 H84 12 17
-
OG360 100 H96 12 16
Features
SMALL RADIUS OMNI-GRID® 360 75 WELD
BELTS THAT RUN SMOOTHER, STRONGER, LONGER
BELTS THAT RUN SMOOTHER, STRONGER, LONGER
SPIRAL
LOTENSION
HYGENIC
TIGHT, 1.1 TURN RATIO FOR SMALL FOOTPRINT OPERATIONS
Small Radius Omni-Grid conveyor belts can negotiate a much tighter turn than regular Omni-Grid belts. In general, the inside radius can be equal to 1.1 times the belt width, making Small Radius Omni-Grid ideal for use in applications where floor space is limited. Small Radius Omni-Grid can turn either left or right, pivoting about a center link.
Omni-Grid® 360 Weld Link
Competitor Link
DIRECTION
Proven Reliability
All Ashworth belts are rated for 100,000 cycles versus competition ratings of only 50,000 cycles
Added Strength & Easy to Clean
Patent pending zero-tension, 360° buttonless welds increase load bearing capacity and are easier to clean versus traditional bridge welds
Reduced Wear
Patented “protrusion leg” design enables the belt to run smoother with less system wear
Increased Belt Life
Patented coining feature reduces run-in wear and increases belt life
Does this meet your project needs?
Does this meet your project needs?
Does this meet your project needs?
Let’s get started!
Let’s get started!
Let’s get started!
Specifications
Technical Specifications
Select another product option
Technical Specifications | Units | Small Radius Omni-Grid® 360 075 |
---|---|---|
Turn Ratio | 1.1-2.0 | |
Pitch | in. [mm] | 0.75 [19.0] |
Available Widths: Curve/Spiral | in. [mm] | 12-48 (304.8-1219) |
Available Widths: Straight Run | in. [mm] | 12-48 (304.8-1219.2) |
Link Height | in. [mm] | 0.44 [11.1] |
Rod Diameter/Material | in. [mm] | 0.192 (4.9) Metal |
Conveying Surface | in. [mm] | Width -1.50 [-38.10] |
Allowable Tension (Curve/Spiral) | lb. [kg] | 150 [68] at 100,000 cycles |
Allowable Tension (Straight Run) | lb. [kg] | 300 [136] at 100,000 cycles |
Turn Direction | Uni-directional (left or right-must specify direction) | |
Mode of Turning | Inside edge collapses in turn | |
Method of Drive | Sprockets driven on links |
Available Sprocket Options
Sprocket Reference
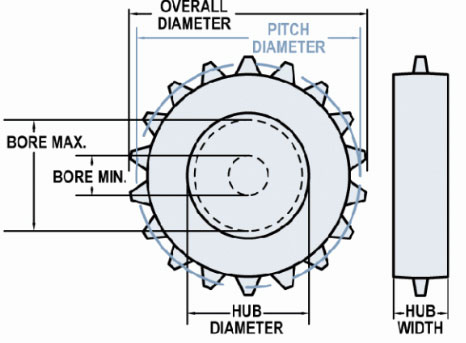
Select another sprocket size
Select a product
Nom. Size | Display | Teeth | Pitch Diameter in (mm) | Hub Diameter in (mm) | Bore Min in (mm) | Bore Max in (mm) |
---|---|---|---|---|---|---|
3 | #3-12 Hardened Steel | 12 | 2.9 (73.66) | 2.36 (59.94) | 1 (25.4) | 1.8 (45.72) |
3 | #3-12 Hardened Steel | 12 | 2.9 (73.66) | 2.36 (59.94) | 1 (25.4) | 1.8 (45.72) |
3 | #3-12 T303 | 12 | 2.9 (73.66) | 2.36 (59.94) | 1 (25.4) | 1.8 (45.72) |
3 | #3-12 T303 | 12 | 2.9 (73.66) | 2.36 (59.94) | 0.94 (23.81) | 1.8 (45.72) |
3 | #3-12 UHMW | 12 | 2.9 (73.66) | 2.25 (57.15) | 0 | 1.5 (38.1) |
3 | #3-16 UHMW | 16 | 3.84 (97.63) | 3 (76.2) | 1.58 (40.01) | 2.13 (54.1) |
3 | #3-16 UHMW | 16 | 3.84 (97.64) | 3 (76.2) | 1 (25.4) | 2.13 (54.1) |
4 | #4-17 T303 | 17 | 4.08 (103.68) | 3.58 (90.81) | 0 | 2.83 (71.88) |
4 | #4-17 UHMW | 17 | 4.08 (103.68) | 3.58 (90.81) | 0.75 (19.05) | 2.58 (65.53) |
4 | #4-17 UHMW | 17 | 4.08 (103.68) | 3.58 (90.81) | 1 (25.4) | 2.58 (65.53) |
4 | #4-18 T303 | 18 | 4.32 (109.68) | 3.82 (96.9) | 0 | 2.95 (74.93) |
4 | #4-18 T303 | 18 | 4.32 (109.68) | 3.82 (96.9) | 1.58 (40.01) | 2.82 (71.63) |
5 | #5-19 UHMW | 19 | 4.56 (115.75) | 4.06 (103.05) | 0.75 (19.05) | 2.94 (74.68) |
5 | #5-21 T303 | 21 | 5.03 (127.81) | 4.54 (115.27) | 1 (25.4) | 3.55 (90.17) |
5 | #5-21 UHMW | 21 | 5.03 (127.81) | 4.54 (115.27) | 1 (25.4) | 3.42 (86.87) |
5 | #5-21 UHMW FS | 21 | 4.79 (121.67) | 4.54 (115.32) | 1 (25.4) | 3.42 (86.87) |
6 | #6 UHMW FI | 0 | 0 | 6 (152.4) | 0.75 (19.05) | 4.64 (117.86) |
6 | #6 UHMW I | 0 | 0 | 6 (152.4) | 0.75 (19.05) | 4.64 (117.86) |
6 | #6-25 T303 | 25 | 5.98 (151.99) | 5.5 (139.67) | 0 | 4.39 (111.51) |
6 | #6-25 T303 | 25 | 5.98 (151.99) | 5.5 (139.67) | 0.5 (12.7) | 4.39 (111.51) |
6 | #6-25 UHMW | 25 | 5.98 (151.99) | 5.5 (139.67) | 0.88 (22.22) | 4.14 (105.16) |
6 | #6-26 T303 | 26 | 6.22 (158.04) | 5.73 (145.64) | 0 | 4.62 (117.35) |
6 | #6-26 T303 | 26 | 6.22 (158.04) | 5.73 (145.64) | 1.58 (40.01) | 4.62 (117.35) |
6 | #6-26 T303 | 26 | 6.22 (158.04) | 5.73 (145.64) | 1.58 (40.01) | 4.62 (117.35) |
6 | #6-26 UHMW | 26 | 6.22 (158.04) | 5.73 (145.64) | 1 (25.4) | 4.37 (111) |
6 | #6-27 UHMW | 27 | 6.42 (163.12) | 5.97 (151.61) | 0.88 (22.22) | 4.61 (117.09) |
8 | #8-34 UHMW | 34 | 8.13 (206.45) | 7.66 (194.46) | 1 (25.4) | 5.93 (150.62) |
3/4" pitch Omni-Grid can use #60 roller chain sprockets modified as follows:
- Face off sprocket such that the overall tooth width is 5/16 (7/94)
- Chamfer corners of the newly machined teeth
* Steel stock sprocket. More available upon request
*Maximum bores provide adequate material thickness for standard keyway. Specify special sized to be used when necessary.
Material Reference
- Acetal - polyoxymethylene plastic
- Celcon - acetal copolymer
- CI - cast iron
- Hardened Steel
- Nylon
- T303 - stainless steel
- T316 - stainless steel
- UMHW - polyethylene plastic
Belt Calculator
No Results
Base Belt Weight
Belt Pitch
Turn Ratio
Belt Strength
Min Filler Roll Diameter
Conveying Surface
Inside Conveying Surface
Outside Conveying Surface
Mesh Opening Size
Open Area Surface
Open Area Thru
Need more detailed information?
Need more detailed information?
Need more detailed information?
Options
Product Options
Omni-Tough Mesh Overlay
- Stainless steel, spring wire, spiral overlay available in 16 and 17 wire gauges.
- 2-1/2 times stronger and more damage-resistant than conventional wire overlays.
- Provides a flatter surface than standard overlays.
- More resistant to product sticking in freezer application.
Designation
B/U X - Y - Z
- B/U = Balanced or Unilateral Weave
- X = Number of Loops/Foot of Width
- Y = Number of Spirals/Foot of Length
- Z = Wire Gauge of Overlay
Examples:
B30-16-16
U42-16-17
Need more detailed information?
Need more detailed information?
Need more detailed information?
Downloads
Downloads
Technical Bulletins
Installation, Assembly & Maintenance Instructions
Conveyor System Review Form
Illustrations
-
ROD ONLY OG360 WELD 075
-
B18-16-16 OG360 WELD 075
-
B30-16-16 OG360 WELD 075
-
B36-16-16 OG360 WELD 075
-
B42-16-16 OG360 WELD 075
-
B48-16-16 OG360 WELD 075
-
B54-16-16 OG360 WELD 075
-
B72-16-16 OG360 WELD 075
-
ROD ONLY OG360 WELD 100
-
B18-12-16 OG360 WELD 100
-
B24-12-16 OG360 WELD 100
-
B30-12-16 OG360 WELD 100
-
B36-12-16 OG360 WELD 100
-
B42-12-16 OG360 WELD 100
-
B48-12-16 OG360 WELD 100
-
B54-12-16 OG360 WELD 100
-
B60-12-16 OG360 WELD 100
-
B72-12-16 OG360 WELD 100
-
U48-12-17 OG360 WELD 100
-
U60-12-16 OG360 WELD 100
-
U72-12-16 OG360 WELD 100
-
ROD ONLY OG360 WELD 150
-
B18-8-16 OG360 WELD 150
-
B24-8-16 OG360 WELD 150
-
B24-8-17 OG360 WELD 150 IGE
-
B30-8-16 OG360 WELD 150
-
B36-8-16 OG360 WELD 150
-
B42-8-16 OG360 WELD 150
-
B54-8-16 OG360 WELD 150
-
B72-8-17 OG360 WELD 150
-
U48-8-16 OG360 WELD 150
-
U54-8-17 OG360 WELD 150
-
OG360 100 H96 12 17
-
OG360 100 Rod Only
-
OG360 100 U48 12 17
-
OG360 100 U54 12 16
-
OG360 100 U54 12 17
-
OG360 100 U60 12 16
-
OG360 100 U60 12 17
-
OG360 100 U72 12 16
-
OG360 100 U72 12 17
-
OG360 150 B18 8 16
-
OG360 150 B18 8 17
-
OG360 150 B24 8 16
-
OG360 150 B24 8 17
-
OG360 150 B30 8 16
-
OG360 150 B30 8 17
-
OG360 150 B36 8 16
-
OG360 150 B36 8 17
-
OG360 150 B42 8 16
-
OG360 150 B42 8 17
-
OG360 150 B54 8 16
-
OG360 150 B54 8 17
-
OG360 150 B72 8 17
-
OG360 150 Rod Only
-
OG360 150 U36 8 16
-
OG360 150 U48 8 16
-
OG360 150 U48 8 17
-
OG360 150 U54 8 16
-
OG360 150 U54 8 17
-
OG360 075 B18 16 16
-
OG360 075 B24 16 16
-
OG360 075 B24 16 17
-
OG360 075 B30 16 16
-
OG360 075 B30 16 17
-
OG360 075 B36 16 16
-
OG360 075 B36 16 17
-
OG360 075 B42 16 16
-
OG360 075 B42 16 17
-
OG360 075 B48 16 16
-
OG360 075 B48 16 17
-
OG360 075 B54 16 16
-
OG360 075 B54 16 17
-
OG360 075 B60 16 16
-
OG360 075 B60 16 17
-
OG360 075 B72 16 16
-
OG360 075 B72 16 17
-
OG360 075 H106 16 16
-
OG360 075 H106 16 17
-
OG360 075 H60 16 16
-
OG360 075 H60 16 17
-
OG360 075 H72 16 16
-
OG360 075 H72 16 17
-
OG360 075 H84 16 16
-
OG360 075 H84 16 17
-
OG360 075 H96 16 16
-
OG360 075 H96 16 17
-
OG360 075 NO MESH
-
OG360 075 Rod Only
-
OG360 075 U36 16 16
-
OG360 100 B30 12 17
-
OG360 100 B18 12 16
-
OG360 100 B18 12 17
-
OG360 100 B24 12 16
-
OG360 100 B24 12 17
-
OG360 100 B30 12 16
-
OG360 100 B36 12 16
-
OG360 100 B36 12 17
-
OG360 100 B42 12 16
-
OG360 100 B42 12 17
-
OG360 100 B48 12 16
-
OG360 100 B48 12 17
-
OG360 100 B54 12 16
-
OG360 100 B54 12 17
-
OG360 100 B60 12 16
-
OG360 100 B60 12 17
-
OG360 100 B72 12 16
-
OG360 100 B72 12 17
-
OG360 100 H106 12 16
-
OG360 100 H106 12 17
-
OG360 100 H60 12 16
-
OG360 100 H60 12 17
-
OG360 100 H72 12 16
-
OG360 100 H72 12 17
-
OG360 100 H84 12 16
-
OG360 100 H84 12 17
-
OG360 100 H96 12 16
Features
SMALL RADIUS OMNI-GRID® 360 100 WELD
BELTS THAT RUN SMOOTHER, STRONGER, LONGER
BELTS THAT RUN SMOOTHER, STRONGER, LONGER
SPIRAL
LOTENSION
HYGENIC
TIGHT, 1.1 TURN RATIO FOR SMALL FOOTPRINT OPERATIONS
Small Radius Omni-Grid conveyor belts can negotiate a much tighter turn than regular Omni-Grid belts. In general, the inside radius can be equal to 1.1 times the belt width, making Small Radius Omni-Grid ideal for use in applications where floor space is limited. Small Radius Omni-Grid can turn either left or right, pivoting about a center link.
Omni-Grid® 360 Weld Link
Competitor Link
DIRECTION
Proven Reliability
All Ashworth belts are rated for 100,000 cycles versus competition ratings of only 50,000 cycles
Added Strength & Easy to Clean
Patent pending zero-tension, 360° buttonless welds increase load bearing capacity and are easier to clean versus traditional bridge welds
Reduced Wear
Patented “protrusion leg” design enables the belt to run smoother with less system wear
Increased Belt Life
Patented coining feature reduces run-in wear and increases belt life
Does this meet your project needs?
Does this meet your project needs?
Does this meet your project needs?
Let’s get started!
Let’s get started!
Let’s get started!
Specifications
Technical Specifications
Select another product option
Technical Specifications | Units | Small Radius Omni-Grid® 360 100 |
---|---|---|
Turn Ratio | 1-2.0 | |
Pitch | in. [mm] | 1.08 [27.4] |
Available Widths: Curve/Spiral | in. [mm] | 12-48 (304.8-1219) |
Available Widths: Straight Run | in. [mm] | 12-48 (304.8-1219.2) |
Link Height | in. [mm] | 0.50 [12.7] |
Rod Diameter/Material | in. [mm] | 0.192 (4.9) Metal |
Conveying Surface | in. [mm] | Width -1.77 [-44.96] |
Allowable Tension (Curve/Spiral) | lb. [kg] | 150 [68] at 100,000 cycles |
Allowable Tension (Straight Run) | lb. [kg] | 300 [136] at 100,000 cycles |
Turn Direction | Uni-directional (left or right-must specify direction) | |
Mode of Turning | Inside edge collapses in turn | |
Method of Drive | Sprockets driven on links |
Available Sprocket Options
Sprocket Reference
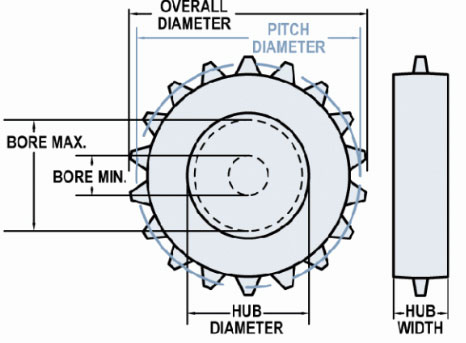
Select another sprocket size
Select a product
Nom. Size | Display | Teeth | Pitch Diameter in (mm) | Hub Diameter in (mm) | Bore Min in (mm) | Bore Max in (mm) |
---|---|---|---|---|---|---|
3 | #3-9 Hardened Steel | 9 | 0 | 2.45 (62.23) | 1 (25.4) | 1.83 (46.48) |
3 | #3-9 T303 | 9 | 3.16 (80.26) | 2.46 (62.48) | 1 (25.4) | 1.84 (46.74) |
3 | #3-9 T303 | 9 | 3.16 (80.26) | 2.46 (62.48) | 1 (25.4) | 1.84 (46.74) |
3 | #3-9 T303 | 9 | 3.16 (80.26) | 2.46 (62.48) | 1.25 (31.75) | 1.84 (46.74) |
3 | #3-9 T303 | 9 | 3.16 (80.26) | 2.46 (62.48) | 0.94 (23.81) | 1.84 (46.74) |
3 | #3-9 T316 | 9 | 3.16 (80.26) | 2.46 (62.48) | 1.44 (36.51) | 1.84 (46.74) |
3 | #3-9 UHMW | 9 | 3.16 (80.26) | 2.53 (64.26) | 1 (25.4) | 1.72 (43.69) |
3 | #3-9 UHMW | 9 | 3.16 (80.26) | 2.53 (64.26) | 0 | 1.72 (43.69) |
4 | #4 UHMW FI | 0 | 0 | 3.92 (99.57) | 0.75 (19.05) | 2.93 (74.42) |
4 | #4 UHMW I | 0 | 0 | 3.92 (99.57) | 0 | 2.93 (74.42) |
4 | #4-11 T303 | 11 | 3.83 (97.36) | 3.18 (80.72) | 0 | 2.07 (52.58) |
4 | #4-11 T303 | 11 | 3.83 (97.36) | 3.18 (80.72) | 0 | 2.44 (61.98) |
4 | #4-12 T303 | 12 | 4.17 (105.97) | 3.54 (89.92) | 0 | 2.8 (71.12) |
4 | #4-12 T316 | 12 | 4.17 (105.97) | 3.54 (89.92) | 0 | 2.8 (71.12) |
4 | #4-12 UHMW | 12 | 4.17 (105.97) | 3.45 (87.63) | 0.75 (19.05) | 2.46 (62.48) |
4 | #4-13 Celcon | 13 | 4.4 (111.76) | 3.9 (99.06) | 1 (25.4) | 2.91 (73.91) |
4 | #4-13 CI | 13 | 4.53 (115.09) | 3.91 (99.22) | 0 | 3.04 (77.22) |
4 | #4-13 T316 | 13 | 4.53 (115.09) | 3.91 (99.22) | 0 | 3.04 (77.22) |
4 | #4-13 UHMW | 13 | 4.53 (115.06) | 3.9 (99.06) | 1 (25.4) | 2.91 (73.91) |
5 | #5-15 T303 | 15 | 5.2 (131.95) | 4.58 (116.36) | 0 | 3.59 (91.19) |
5 | #5-15 UHMW | 15 | 5.2 (131.95) | 4.58 (116.36) | 2 (50.8) | 3.46 (87.88) |
6 | #6 UHMW FI | 0 | 0 | 5.65 (143.51) | 0.75 (19.05) | 4.29 (108.97) |
6 | #6 UHMW I | 0 | 0 | 5.65 (143.51) | 0 | 4.29 (108.97) |
6 | #6-18 CI | 18 | 6.24 (158.5) | 5.66 (143.67) | 0 | 3.75 (95.25) |
6 | #6-18 Nylon | 18 | 6.24 (158.5) | 5.65 (143.51) | 1 (25.4) | 4.54 (115.32) |
6 | #6-18 T316 | 18 | 6.24 (158.5) | 5.66 (143.67) | 1 (25.4) | 3.75 (95.25) |
6 | #6-18 UHMW | 18 | 6.24 (158.5) | 5.65 (143.51) | 0 | 4.29 (108.97) |
6 | #6-18 UHMW FS | 18 | 6.15 (156.16) | 5.65 (143.46) | 0 | 4.29 (108.97) |
6 | #6-18 UHMW Product Release | 18 | 6.4 (162.51) | 5.65 (143.46) | 1 (25.4) | 4.29 (108.97) |
6 | #6-18 UHMW Split | 18 | 6.24 (158.5) | 5.65 (143.46) | 0 | 4.29 (108.97) |
6 | #6-19 T303 | 19 | 6.55 (166.47) | 6.03 (153.21) | 0 | 4.8 (121.92) |
6 | #6-19 UHMW | 19 | 6.55 (166.47) | 6.03 (153.21) | 1.18 (30) | 4.67 (118.62) |
8 | #8 UHMW FI | 0 | 0 | 7.38 (187.45) | 0.75 (19.05) | 5.89 (149.61) |
8 | #8 UHMW I | 0 | 0 | 7.38 (187.45) | 0 | 5.89 (149.61) |
8 | #8-23 CI | 23 | 7.41 (188.11) | 7.41 (188.11) | 0 | 5.9 (149.86) |
8 | #8-23 CI | 23 | 7.96 (202.18) | 7.41 (188.12) | 0 | 4.75 (120.65) |
8 | #8-23 T316 | 23 | 7.96 (202.18) | 7.41 (188.12) | 0 | 4.75 (120.65) |
8 | #8-23 T316 | 23 | 7.97 (202.41) | 7.41 (188.12) | 1 (25.4) | 4.75 (120.65) |
8 | #8-23 UHMW | 23 | 7.96 (202.18) | 7.39 (187.71) | 1 (25.4) | 5.9 (149.86) |
8 | #8-23 UHMW Split | 23 | 7.89 (200.33) | 7.39 (187.63) | 0 | 5.9 (149.86) |
10 | #10-31 CI | 31 | 10.72 (272.29) | 10.16 (258.06) | 0 | 8.67 (220.22) |
10 | #10-31 T316 | 31 | 10.72 (272.29) | 10.16 (258.06) | 0 | 8.67 (220.22) |
10 | #10-31 UHMW | 31 | 10.66 (270.76) | 10.16 (258.06) | 0.99 (25.02) | 8.42 (213.87) |
12 | #12-37 UHMW | 37 | 12.74 (323.49) | 12.24 (310.79) | 0.99 (25.02) | 10.49 (266.45) |
* Stock sprockets: UHMWPE, Steel. More available upon request
*Maximum bores provide adequate material thickness for standard keyway. Specify special sized to be used when necessary.
Material Reference
- Acetal - polyoxymethylene plastic
- Celcon - acetal copolymer
- CI - cast iron
- Hardened Steel
- Nylon
- T303 - stainless steel
- T316 - stainless steel
- UMHW - polyethylene plastic
Need more detailed information?
Need more detailed information?
Need more detailed information?
Belt Calculator
No Results
Base Belt Weight
Belt Pitch
Turn Ratio
Belt Strength
Min Filler Roll Diameter
Conveying Surface
Inside Conveying Surface
Outside Conveying Surface
Mesh Opening Size
Open Area Surface
Open Area Thru
Need more detailed information?
Need more detailed information?
Need more detailed information?
Options
Product Options
Omni-Tough Mesh Overlay
- Stainless steel, spring wire, spiral overlay available in 16 and 17 wire gauges.
- 2-1/2 times stronger and more damage-resistant than conventional wire overlays.
- Provides a flatter surface than standard overlays.
- More resistant to product sticking in freezer application.
Designation
B/U X - Y - Z
- B/U = Balanced or Unilateral Weave
- X = Number of Loops/Foot of Width
- Y = Number of Spirals/Foot of Length
- Z = Wire Gauge of Overlay
Examples:
B30-16-16
U42-16-17
Need more detailed information?
Need more detailed information?
Need more detailed information?
Downloads
Downloads
Technical Bulletins
Installation, Assembly & Maintenance Instructions
Conveyor System Review Form
Illustrations
-
ROD ONLY OG360 WELD 075
-
B18-16-16 OG360 WELD 075
-
B30-16-16 OG360 WELD 075
-
B36-16-16 OG360 WELD 075
-
B42-16-16 OG360 WELD 075
-
B48-16-16 OG360 WELD 075
-
B54-16-16 OG360 WELD 075
-
B72-16-16 OG360 WELD 075
-
ROD ONLY OG360 WELD 100
-
B18-12-16 OG360 WELD 100
-
B24-12-16 OG360 WELD 100
-
B30-12-16 OG360 WELD 100
-
B36-12-16 OG360 WELD 100
-
B42-12-16 OG360 WELD 100
-
B48-12-16 OG360 WELD 100
-
B54-12-16 OG360 WELD 100
-
B60-12-16 OG360 WELD 100
-
B72-12-16 OG360 WELD 100
-
U48-12-17 OG360 WELD 100
-
U60-12-16 OG360 WELD 100
-
U72-12-16 OG360 WELD 100
-
ROD ONLY OG360 WELD 150
-
B18-8-16 OG360 WELD 150
-
B24-8-16 OG360 WELD 150
-
B24-8-17 OG360 WELD 150 IGE
-
B30-8-16 OG360 WELD 150
-
B36-8-16 OG360 WELD 150
-
B42-8-16 OG360 WELD 150
-
B54-8-16 OG360 WELD 150
-
B72-8-17 OG360 WELD 150
-
U48-8-16 OG360 WELD 150
-
U54-8-17 OG360 WELD 150
-
OG360 100 H96 12 17
-
OG360 100 Rod Only
-
OG360 100 U48 12 17
-
OG360 100 U54 12 16
-
OG360 100 U54 12 17
-
OG360 100 U60 12 16
-
OG360 100 U60 12 17
-
OG360 100 U72 12 16
-
OG360 100 U72 12 17
-
OG360 150 B18 8 16
-
OG360 150 B18 8 17
-
OG360 150 B24 8 16
-
OG360 150 B24 8 17
-
OG360 150 B30 8 16
-
OG360 150 B30 8 17
-
OG360 150 B36 8 16
-
OG360 150 B36 8 17
-
OG360 150 B42 8 16
-
OG360 150 B42 8 17
-
OG360 150 B54 8 16
-
OG360 150 B54 8 17
-
OG360 150 B72 8 17
-
OG360 150 Rod Only
-
OG360 150 U36 8 16
-
OG360 150 U48 8 16
-
OG360 150 U48 8 17
-
OG360 150 U54 8 16
-
OG360 150 U54 8 17
-
OG360 075 B18 16 16
-
OG360 075 B24 16 16
-
OG360 075 B24 16 17
-
OG360 075 B30 16 16
-
OG360 075 B30 16 17
-
OG360 075 B36 16 16
-
OG360 075 B36 16 17
-
OG360 075 B42 16 16
-
OG360 075 B42 16 17
-
OG360 075 B48 16 16
-
OG360 075 B48 16 17
-
OG360 075 B54 16 16
-
OG360 075 B54 16 17
-
OG360 075 B60 16 16
-
OG360 075 B60 16 17
-
OG360 075 B72 16 16
-
OG360 075 B72 16 17
-
OG360 075 H106 16 16
-
OG360 075 H106 16 17
-
OG360 075 H60 16 16
-
OG360 075 H60 16 17
-
OG360 075 H72 16 16
-
OG360 075 H72 16 17
-
OG360 075 H84 16 16
-
OG360 075 H84 16 17
-
OG360 075 H96 16 16
-
OG360 075 H96 16 17
-
OG360 075 NO MESH
-
OG360 075 Rod Only
-
OG360 075 U36 16 16
-
OG360 100 B30 12 17
-
OG360 100 B18 12 16
-
OG360 100 B18 12 17
-
OG360 100 B24 12 16
-
OG360 100 B24 12 17
-
OG360 100 B30 12 16
-
OG360 100 B36 12 16
-
OG360 100 B36 12 17
-
OG360 100 B42 12 16
-
OG360 100 B42 12 17
-
OG360 100 B48 12 16
-
OG360 100 B48 12 17
-
OG360 100 B54 12 16
-
OG360 100 B54 12 17
-
OG360 100 B60 12 16
-
OG360 100 B60 12 17
-
OG360 100 B72 12 16
-
OG360 100 B72 12 17
-
OG360 100 H106 12 16
-
OG360 100 H106 12 17
-
OG360 100 H60 12 16
-
OG360 100 H60 12 17
-
OG360 100 H72 12 16
-
OG360 100 H72 12 17
-
OG360 100 H84 12 16
-
OG360 100 H84 12 17
-
OG360 100 H96 12 16
Features
OMNI-GRID® 360 75 WELD
OMNI-GRID® 360 75 WELD
HIGH DENSITY MESH
HIGH DENSITY MESH
BELTS THAT RUN SMOOTHER, STRONGER, LONGER
BELTS THAT RUN SMOOTHER, STRONGER, LONGER
SPIRAL
LOTENSION
HYGENIC
TIGHT, 1.1 TURN RATIO FOR SMALL FOOTPRINT OPERATIONS
Small Radius Omni-Grid conveyor belts can negotiate a much tighter turn than regular Omni-Grid belts. In general, the inside radius can be equal to 1.1 times the belt width, making Small Radius Omni-Grid ideal for use in applications where floor space is limited. Small Radius Omni-Grid can turn either left or right, pivoting about a center link.
Omni-Grid® 360 Weld Link
Competitor Link
DIRECTION
APPLICATIONS
Proven Reliability
All Ashworth belts are rated for 100,000 cycles versus competition ratings of only 50,000 cycles
Added Strength & Easy to Clean
Patent pending zero-tension, 360° buttonless welds increase load bearing capacity and are easier to clean versus traditional bridge welds
Reduced Wear
Patented “protrusion leg” design enables the belt to run smoother with less system wear
Increased Belt Life
Patented coining feature reduces run-in wear and increases belt life
Does this meet your project needs?
Does this meet your project needs?
Does this meet your project needs?
Let’s get started!
Let’s get started!
Let’s get started!
Specifications
Technical Specifications
Select another product option
Technical Specifications | Units | OMNI-GRID® 360 75 - HIGH DENSITY MESH |
---|---|---|
Turn Ratio | 0-0.0 | |
Pitch | in. [mm] | 0.75 [19.0] |
Available Widths: Curve/Spiral | in. [mm] | 12-40 (304.8-1016) |
Available Widths: Straight Run | in. [mm] | 12-60 (304.8-1524.0) |
Link Height | in. [mm] | 0.44 [11.1] |
Rod Diameter/Material | in. [mm] | 0.192 (4.9) Metal |
Conveying Surface | in. [mm] | Width -2.23 [-56.64] |
Allowable Tension (Curve/Spiral) | lb. [kg] | 200 [91] at 100,000 cycles |
Allowable Tension (Straight Run) | lb. [kg] | 400 [181] at 100,000 cycles |
Turn Direction | Bi-directional | |
Mode of Turning | Inside edge collapses in turn | |
Method of Drive | Sprockets driven on links |
Belt Calculator
No Results
Base Belt Weight
Belt Pitch
Turn Ratio
Belt Strength
Min Filler Roll Diameter
Conveying Surface
Inside Conveying Surface
Outside Conveying Surface
Mesh Opening Size
Open Area Surface
Open Area Thru
Need more detailed information?
Need more detailed information?
Need more detailed information?
Options
Product Options
Omni-Tough Mesh Overlay
- Stainless steel, spring wire, spiral overlay available in 16 and 17 wire gauges.
- 2-1/2 times stronger and more damage-resistant than conventional wire overlays.
- Provides a flatter surface than standard overlays.
- More resistant to product sticking in freezer application.
Designation
B/U X - Y - Z
- B/U = Balanced or Unilateral Weave
- X = Number of Loops/Foot of Width
- Y = Number of Spirals/Foot of Length
- Z = Wire Gauge of Overlay
Examples:
B30-16-16
U42-16-17
Downloads
Downloads
Technical Bulletins
Installation, Assembly & Maintenance Instructions
Conveyor System Review Form
Illustrations
-
ROD ONLY OG360 WELD 075
-
B18-16-16 OG360 WELD 075
-
B30-16-16 OG360 WELD 075
-
B36-16-16 OG360 WELD 075
-
B42-16-16 OG360 WELD 075
-
B48-16-16 OG360 WELD 075
-
B54-16-16 OG360 WELD 075
-
B72-16-16 OG360 WELD 075
-
ROD ONLY OG360 WELD 100
-
B18-12-16 OG360 WELD 100
-
B24-12-16 OG360 WELD 100
-
B30-12-16 OG360 WELD 100
-
B36-12-16 OG360 WELD 100
-
B42-12-16 OG360 WELD 100
-
B48-12-16 OG360 WELD 100
-
B54-12-16 OG360 WELD 100
-
B60-12-16 OG360 WELD 100
-
B72-12-16 OG360 WELD 100
-
U48-12-17 OG360 WELD 100
-
U60-12-16 OG360 WELD 100
-
U72-12-16 OG360 WELD 100
-
ROD ONLY OG360 WELD 150
-
B18-8-16 OG360 WELD 150
-
B24-8-16 OG360 WELD 150
-
B24-8-17 OG360 WELD 150 IGE
-
B30-8-16 OG360 WELD 150
-
B36-8-16 OG360 WELD 150
-
B42-8-16 OG360 WELD 150
-
B54-8-16 OG360 WELD 150
-
B72-8-17 OG360 WELD 150
-
U48-8-16 OG360 WELD 150
-
U54-8-17 OG360 WELD 150
-
OG360 100 H96 12 17
-
OG360 100 Rod Only
-
OG360 100 U48 12 17
-
OG360 100 U54 12 16
-
OG360 100 U54 12 17
-
OG360 100 U60 12 16
-
OG360 100 U60 12 17
-
OG360 100 U72 12 16
-
OG360 100 U72 12 17
-
OG360 150 B18 8 16
-
OG360 150 B18 8 17
-
OG360 150 B24 8 16
-
OG360 150 B24 8 17
-
OG360 150 B30 8 16
-
OG360 150 B30 8 17
-
OG360 150 B36 8 16
-
OG360 150 B36 8 17
-
OG360 150 B42 8 16
-
OG360 150 B42 8 17
-
OG360 150 B54 8 16
-
OG360 150 B54 8 17
-
OG360 150 B72 8 17
-
OG360 150 Rod Only
-
OG360 150 U36 8 16
-
OG360 150 U48 8 16
-
OG360 150 U48 8 17
-
OG360 150 U54 8 16
-
OG360 150 U54 8 17
-
OG360 075 B18 16 16
-
OG360 075 B24 16 16
-
OG360 075 B24 16 17
-
OG360 075 B30 16 16
-
OG360 075 B30 16 17
-
OG360 075 B36 16 16
-
OG360 075 B36 16 17
-
OG360 075 B42 16 16
-
OG360 075 B42 16 17
-
OG360 075 B48 16 16
-
OG360 075 B48 16 17
-
OG360 075 B54 16 16
-
OG360 075 B54 16 17
-
OG360 075 B60 16 16
-
OG360 075 B60 16 17
-
OG360 075 B72 16 16
-
OG360 075 B72 16 17
-
OG360 075 H106 16 16
-
OG360 075 H106 16 17
-
OG360 075 H60 16 16
-
OG360 075 H60 16 17
-
OG360 075 H72 16 16
-
OG360 075 H72 16 17
-
OG360 075 H84 16 16
-
OG360 075 H84 16 17
-
OG360 075 H96 16 16
-
OG360 075 H96 16 17
-
OG360 075 NO MESH
-
OG360 075 Rod Only
-
OG360 075 U36 16 16
-
OG360 100 B30 12 17
-
OG360 100 B18 12 16
-
OG360 100 B18 12 17
-
OG360 100 B24 12 16
-
OG360 100 B24 12 17
-
OG360 100 B30 12 16
-
OG360 100 B36 12 16
-
OG360 100 B36 12 17
-
OG360 100 B42 12 16
-
OG360 100 B42 12 17
-
OG360 100 B48 12 16
-
OG360 100 B48 12 17
-
OG360 100 B54 12 16
-
OG360 100 B54 12 17
-
OG360 100 B60 12 16
-
OG360 100 B60 12 17
-
OG360 100 B72 12 16
-
OG360 100 B72 12 17
-
OG360 100 H106 12 16
-
OG360 100 H106 12 17
-
OG360 100 H60 12 16
-
OG360 100 H60 12 17
-
OG360 100 H72 12 16
-
OG360 100 H72 12 17
-
OG360 100 H84 12 16
-
OG360 100 H84 12 17
-
OG360 100 H96 12 16